Are you ready for Industry 4.0?
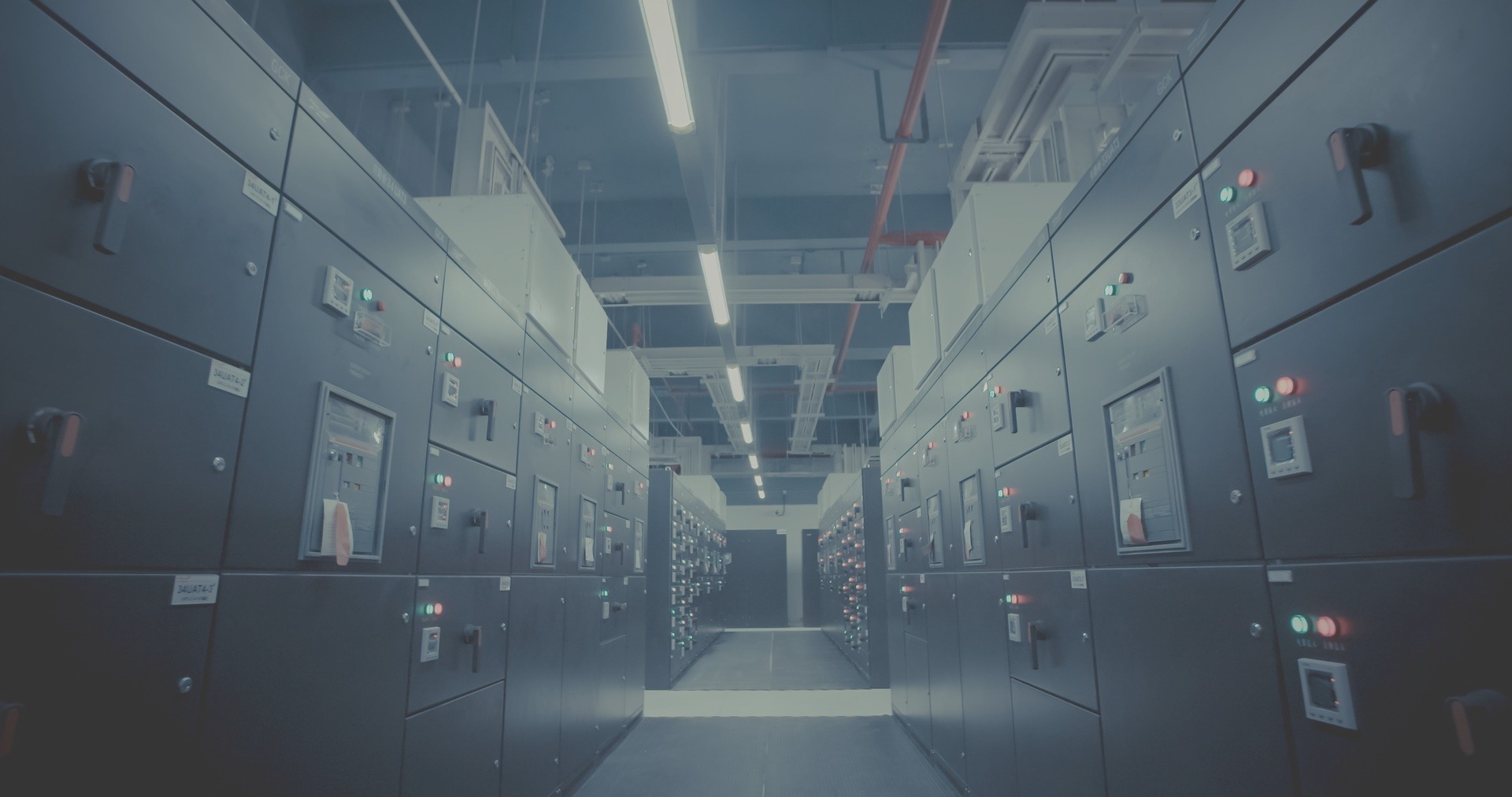
Gary Noble recruitment, supply-chain, Industry 4.0...
There have been three key industrial revolutions to date: the Victorian move from farming to factory production in the 19th Century; the rise of mass production and the early electrification of factories; and the replacement of analogue and mechanical technology with digital technology and the rise of the Internet.
Experts believe we are now on the cusp of a fourth revolution, referred to as Industry 4.0, which has the potential to hugely impact the day to day roles of procurement and supply chain professionals but also affect the talent they need to hire.
What exactly is Industry 4.0?
The basic principle of Industry 4.0 is that by connecting machines and systems, businesses are creating intelligent networks where every part of a chain is linked to and can control other parts.
There are four key technologies involved in this revolution:
- The internet of things (IoT) creates systems to link together parts of a chain and collect data
- The ability to collect and analyse Big Data means that systems can quickly work through huge amounts of data to produce insights that can be acted upon
- Artificial Intelligence allows systems to complete complex tasks more quickly and efficiently than with human intervention
- Having a cloud-based communications infrastructure backing this up, secure enough to be used by industry
So what does this mean for procurement?
Industry 4.0 is already having an impact on supply chains and the continued integration of these technologies is likely to both improve efficiencies within the market and create significant savings.
The idea is that when everything talks to everything else, failures can be predicted before they happen and maintenance processes automatically triggered, or logistics can react to unexpected changed in production. Machines using self-configuration, self-optimisation and artificial intelligence can complete complex tasks in order to deliver better quality goods and services, as well as huge cost efficiencies.
For example, Knapp, an international logistics firm, has already developed a revolutionary optically guided picking system, which directs pickers to each required location using augmented reality. As well as allowing employees to locate items more quickly and precisely, it also allows new staff to be trained extremely quickly, creating a more flexible workforce. The system also means pickers have both hands free to build stronger and more efficient pallets, with fragile items better protected. Implementation has already led to many benefits, including a fall in error rates of 40%, greatly reducing spend on replacement orders.
Won’t this lead to job losses?
Rather than seeing jobs lost, it is actually more likely Industry 4.0 will lead to the creation of new roles. Those employees with traditional skills, such as process mapping analysis and planning, will still be valuable, but firms will also need to bring in technology specialists to help organisations implement innovations to deliver the greatest value.
In fact, the thing most likely to hold businesses taking full advantage of Industry 4.0 is finding and hiring employees with the right skills to put it into practice. Technology specialists are already in short supply in the UK, and there are concerns that Brexit will exacerbate this issue even further by making it harder to bring in workers from the EU. And as Industry 4.0 becomes more embedded and demand for these technology specialists increases even more, these skill shortages are only going to become more acute.
Savvy employers will have to look to other sectors, such as oil and gas, to poach from their stocks of skilled professionals. They will also have to offer their existing employees more training in areas such as AI and big data, to help foster home-grown technology skills. Offering your staff continuing professional development in this way is also a great way to attract entry-level employees, as well as helping to retain experienced talent.
Marco Taisch, director of the executive course in manufacturing management at MIP Politecnico di Milano School of Management, is a leading supply chain academic and a keen proponent of Industry 4.0. He believes that Industry 4.0 will “drive huge and sweeping changes across the entire field and create a much greater need for professionals with advanced technology skills”. He also believes that “these changes will infiltrate into the industry at a rapid pace" and that any firms not preparing to meet the anticipated demand could "rapidly fall behind the curve and start to lose competitiveness without these skills in place”.
It is up to procurement leaders to make sure they don’t fall behind in the war for technology talent and start recruiting today for the world of tomorrow. If you’d like to discuss how 1st Executive can help you get ready for Industry 4.0, why not get in touch on 08432 163030 or email us.